Understanding Supply Chain Analytics
Supply chain analytics refers to the integrated process of collecting, cleaning, transforming, and analyzing data tied to the flow of goods, services, finances, and information across an organization’s supply chain operations.
It encompasses using quantitative methods and technology solutions to derive actionable business insights about supply-demand conditions, production variables, logistics issues, risks events and performance inefficiencies existing within intricate global production, delivery, and distribution ecosystems. Core supply chain analytics components include:
- Using algorithms and statistical modeling on volumes of structured (e.g., transactions, inventory indexes) and unstructured (e.g., emails, documents) data compiling from disparate front-end, back-end, operational and enterprise systems along end-to-end supply chains.
- Leveraging visualization tools transforming complex multivariate analyses into digestible performance dashboards, predictive models and prescriptive recommendations supporting executive strategy decisions or day-to-day supply chain administrative decision-making.
Unlike traditional reactive approaches, modern data-backed supply chain analytics takes a forward-looking, evidence-based methodology toward continually optimizing, adapting, and sustaining operations even amidst volatility, uncertainties and changes impacting interconnected supplier, factory, storage, and logistics networks.
Types of Data Analytics in Supply Chain
- Descriptive Analytics
- Diagnostics Analytics
- Predictive Analytics
- Prescriptive Analytics
Let’s explore the diverse landscape of data analytics in supply chain management to equip you with comprehensive insights. .
Descriptive Analytics
Descriptive analytics summarize “what has happened” across supply chain operations using historical data on execution metrics like manufacturing throughput, inventory levels, transport capacities, energy consumption and sales.
Retailers may assess descriptive reports revealing sales numbers, bestselling products, customer demographics and real-time web traffic dashboards delivering snapshots of past and present performances.
By linking datasets using unique identifiers like stock-keeping units (SKUs), descriptive analytics quantify operational progress toward benchmarks helping supply chain managers troubleshoot misses requiring corrective actions.
Diagnostic Analytics
While descriptive statistics inform “what” occurred at granular levels, diagnostic analytics tackle the “why is it happening” questions around root causes behind emerging or recurrent issues within supply chains. Often combining time series data, diagnostic analyses enhance performances by:
- Pinpointing parts shortages tied to specific supplier geographies disruption events
- Quantifying delays between material arrivals and finished goods inventory buildups indicating production scheduling bottlenecks
- Identifying quality control lapses tracing back to particular machinery faults or factory worker skill gaps
Such insights enable tactical and targeted resolutions preventing future disruptions vs broadly symptomatic treatments after negative commercial impacts materialize.
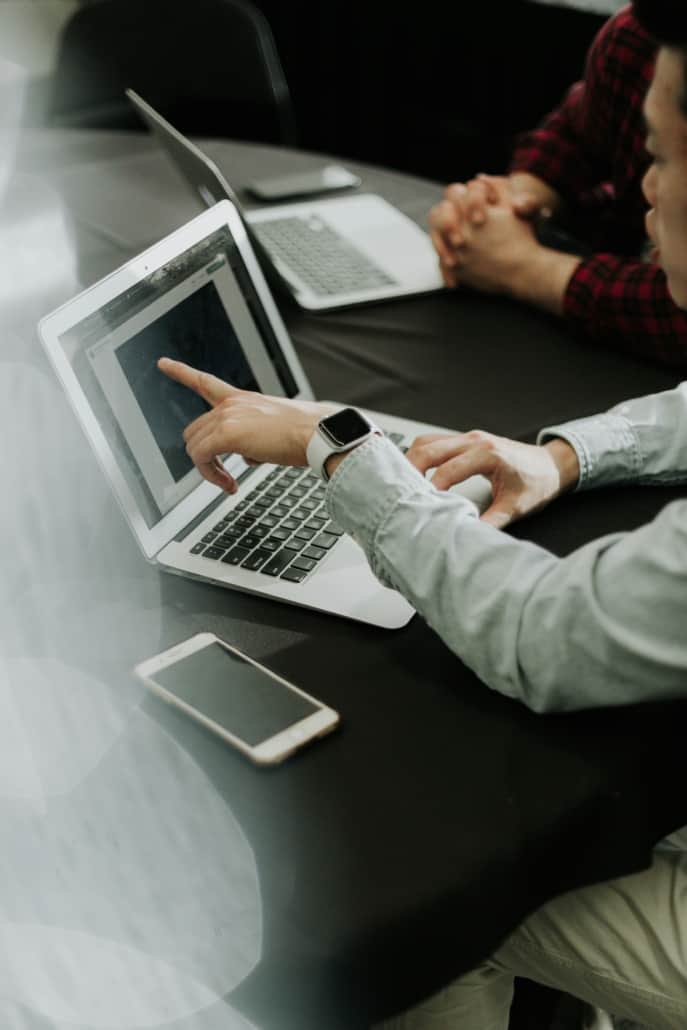
Predictive Analytics
Predictive supply chain analytics forecast “what could happen” based on extrapolating insights from vast data volumes detailing intricate supplier-manufacturer-distributor-retailer networks and market conditions influencing end consumer demand. Sophisticated machine learning algorithms help businesses predict within quantified confidence levels:
- Most likely sales within upcoming holiday seasons
- Probability inventory stock-outs arising from unprecedented demand changes
- Impending part shortages tied to weather risks in supplier countries
By anticipating scenarios weeks and months ahead, enterprises pivot intelligently via orders rebalancing, contracts adjustments, storage repositioning and contingency capacities securing to buffer unpredictabilities.
Prescriptive Analytics
While predictive models envisage uncertainty ranges around demand and supply variability, prescriptive analytics recommend precise counteractions answering “what should businesses do” preempting challenges or capitalizing upon opportunities. Optimization algorithms and simulation models guide executives:
- Ideal manufacturing adaptions aligning production pipelines and inventory buildups with sales forecasts updates
- Most efficient transportation modes and warehousing locations amidst logistics infrastructure shifts
- Optimal commodity hedging and procurement strategies responding to early supply risks indicators
Thus, prescriptive supply chain analytics converts insights into precise executable what-if mitigation, adaptation and growth pathways tailored to enterprise risk appetites, resource capacities and customer preferences.
Advanced analytics uplifts supply chain performance through enhanced visibility revealing operational friction points. Predictive analytics assists inventory and demand synchronization while prescriptive intelligence informs network-wide resilience strategies. Thus, analytics facilitate responsive issue resolution, calibrated forecasting/production and risk mitigation securing customer fulfillment.
Gaining Visibility and Transparency
Supply chain data analytics deliver complete cross-network transparency down to individual transaction statuses using integrated IoT sensors, geospatial tracking and distributed ledger records. Such real-time visibility facilitates identifying:
- Regional logistics bottlenecks creating widespread ripple effects
- Supplier quality control failures necessitating containment actions
- Upstream part shortages requiring production rebalancing
Armed with granular insights into globalized, multi-echelon supply flows, managers swiftly address operational chokepoints through tactic measures like priority shipping reroutes or temporary manufacturer diversification preventing magnified disruptions.
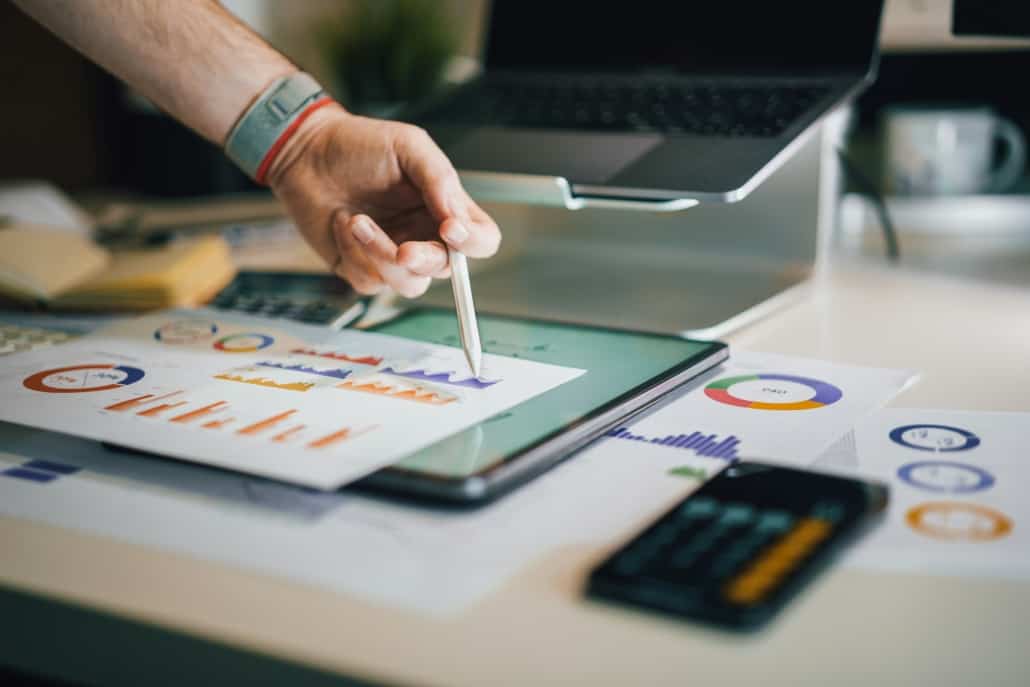
Demand Forecasting and Inventory Management
By aggregating consumption trends, pricing indicators and retail channel sales data, machine learning forecasting algorithms generate highly accurate demand predictions weeks and months ahead. Such reliable projections allow calibrating downstream supply activities accordingly via:
- Optimized manufacturing schedules aligning production volumes with anticipated peak sales
- Proactive safety stock buildups at redistribution centers protecting against demand plan volatility
- Expanded warehouse capacities or extended contracts from third-party logistics firms
Thereby predictive analytics enables calibrating inventory levels judiciously avoiding excessive holding costs or deep revenue losses from stock-outs arising through demand/supply mismatches.
Supplier and Risk Management
Intelligent analytics pours through thousands of external signals assessing potential supplier instability from emerging financial distress, leadership changes, ratings downgrades, bankruptcies, geopolitics and extreme weather threats. Alert dashboards notify supply chain teams of at-risk vendors months earlier prompting preemptive safeguarding through smart mitigations.
Implementing Data Analytics in Your Supply Chain
To launch a supply chain analytics program, operational leaders must coordinate strategically by following a series of methodical build-out phases enabling proper data infrastructures, talent acquisition and solution scalability. Follow these step-by-step guidelines for efficient rollouts:
- Identify business problems and improvement opportunities for analytics goals
- Audit existing data assets and technology systems revealing functionality gaps
- Estimate required analytics investments aligned to organizational priorities
- Recruit data analyst team members through hiring, training or co-sourcing
- Design data collection procedures across departments ensuring consistent inputs
- Standardize datasets applying cleaning rules and master data catalogs
- Select customizable analytics platforms adapting to evolving requirements
- Develop insightful visualizations and real-time alerts conveying analytics findings
- Incorporate findings into decision rules automating responsive issue resolution
- Continually review analytics adoption measuring ROI towards quantified KPIs
Challenges and Solutions
Transforming decisively into data-driven supply chain operations meets inevitable growing pains as analytics initiatives encounter real-world roadblocks that teams must acknowledge then actively resolve through multi-pronged approaches.
Data Quality Issues
Inaccurate, incomplete or inconsistent records drastically undermine analytics utility by producing unreliable insights failing strategy calibration. Data defects arise from:
- Weak input validation checks accepting bad data
- Decentralized management with discrepant standards
- Insufficient master data governance enforcing quality
You can overcome these problems: Invest in data quality tools catching errors through automation. Appoint dedicated data stewards accountable for sustained quality. Incorporate persistent data monitoring at ingestion revealing problems
Data Silos
Consolidating siloed datasets proves fundamental establishing enterprise-wide visibility but requires overcoming entrenched barriers around territorial data owners reluctant relinquishing perceived ownership.
- Functional teams hoarding data they gather reinforcing silos;
- Managers fear shared data enabling oversight fueling resistance;
- IT legacy systems lag modern integrations with band-aid links.
Leadership mandates dismantling fiefdoms through centralized analytics charter. IT architects implement flexible data platforms using APIs and cloud infrastructure. Cross-functional analytics council representation breaks down distrust gradually.
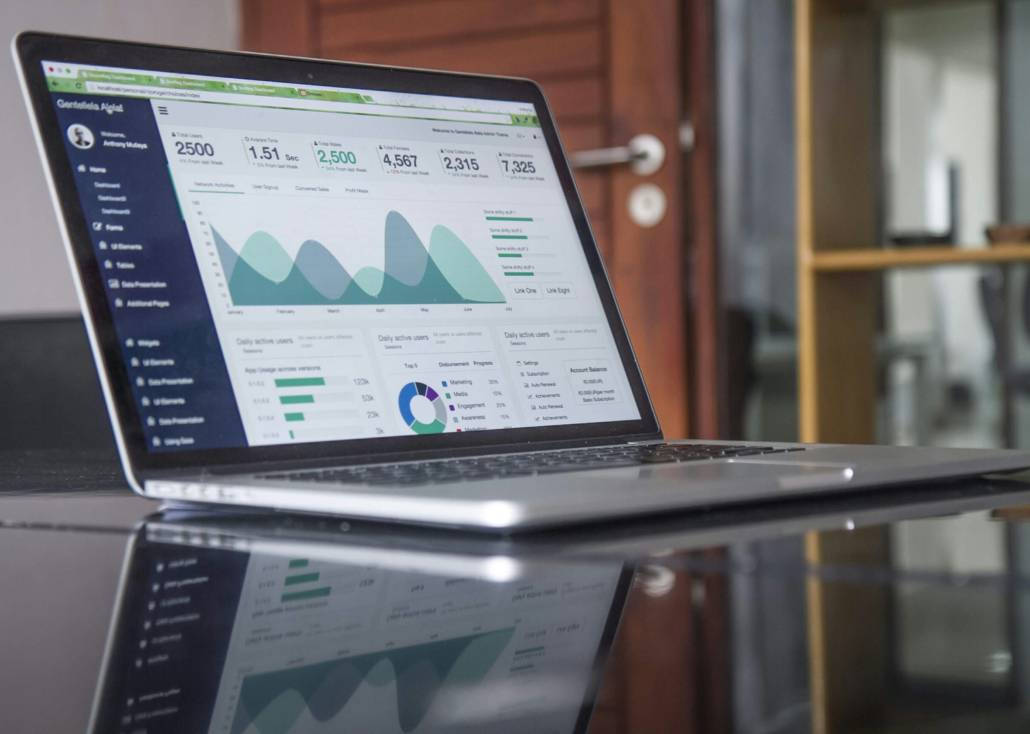
Talent Shortfalls
Data science and analytics still suffer acute talent scarcity with practitioner demand massively outpacing qualified professional supply. Analytics projects’ progress slowly hampered by capability gaps analyzing expansive data.
- Few employees receive adequate analytics skill-building opportunities;
- Compensation lags technology sector limiting recruitment/retention;
- Resource/bandwidth limitations delay deploying tools fully.
Explore machine learning assisted modeling reducing manual modeling. Co-source specialized analytics tasks with competent external partners. Develop internal data academy accelerating analytical competencies
Embedding Insights
Analytics lose impact when operational decisions still get guided intuitionally rather than by data-evidenced algorithms. Leaders must nurture analytical culture valuing decisions supported by intelligence.
- Middle managers brush aside analytics preferring status quo;
- Inconsistent accountability procedures undercuts adoption;
- Lacking automation applies insights manually.
Some solutions include incorporating usage KPIs into performance evaluation frameworks and configuring alerts, triggers and memos maintaining visibility. You must also Integrate dashboards into workflows sustaining usage.
Case Studies and Success Stories
IBM implemented cognitive computing and analytics throughout its global supply chain operations. This transformation helped reduce costs substantially while making the network more agile and resilient.
Specifically, supply chain expenses lowered by $160 million annually after the analytics integration. Throughout even the peak COVID-19 disruptions, IBM maintained 100% order delivery performance ensuring uninterrupted product supplies towards customers.
However, IBM’s supply chain previously relied on fragmented legacy systems scattered across siloed departments that delayed information flows. Harnessing its own emerging analytics solutions, IBM established an integrated data foundation fueling the supply chain modernization.
The recent market uncertainty has exposed many supply chain vulnerabilities across industries. Remote work mandates, unexpected demand fluctuations for certain items, and logistical complexities introduced duress many networks were unprepared for.
Numerous companies suffered profitability impacts from commodity price volatility, shifting consumer demand leading to forecasting errors, and supplier-side supply security issues.
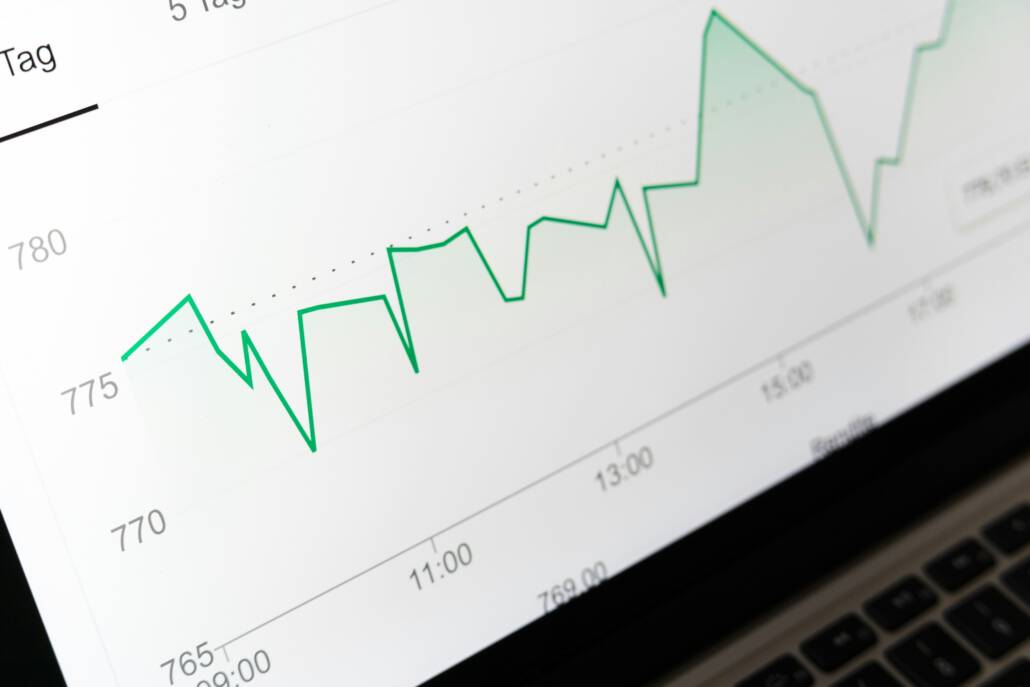
However, by deploying advanced data analytics, businesses can optimize supply chain planning and responses in ways unavailable previously when market variables remained less dynamic. Analytics supports calibration adjustments around manufacturing, inventory, and logistics precisely matching demand in times of turbulence.
The Future of Supply Chain Analytics
Strategic technology trends will shape supply chain advancements in 2024 and beyond. These technologies facilitate leaders controlling operations better and opening up new opportunities leveraging complementary human-machine capabilities.
Integrating Emerging Tech
Gartner expects supply chain leaders will increasingly adopt cutting-edge innovations like IoT sensors, blockchain-based trackers, cloud analytics and artificial intelligence over the next two years. These tools aim helping organizations exert greater control over end-to-end supply flows while also enabling creative human-machine interfaces delivering differentiating value.
Real Time Data Analytics
Oxford research found 51% of supply chain leaders now utilize AI and predictive modeling unlocking data-driven decision support. Additionally, a separate Gartner poll revealed 78% of Chief Supply Chain Officers feel apprehensive about AI impacts on future recruiting skill profiles. Correspondingly, 79% aim expanding analytics and AI training for employees facilitating adoption.
Increased Automation
43% companies will persist digitizing operations by assimilating innovative technologies across organizational ecosystems over the next two years. This indicates automation will continue permeating planning, inventory, logistics and administration activities to varying degrees.
FAQs
What is supply chain analytics?
Supply chain analytics refers to the integrated process of collecting, cleaning, analyzing and visualizing data tied to the end-to-end flow of goods, services, finances and information across an organization’s supply chain ecosystem to generate actionable insights for optimizing operations.
How does data analytics optimize supply chain operations?
Data analytics optimizes supply chain operations by providing enhanced visibility into bottlenecks, automating forecasting models to improve demand-supply synchronization, assessing supplier risks to enable continuity planning, reducing process inefficiencies, and prescribing data-backed recommendations that enhance decision-making.
What are the key benefits of integrating data analytics into the supply chain?
Key benefits include greater visibility improving responsiveness, optimized inventory through demand forecasting, strengthened supplier relationships via performance insights, reduced costs by trimming process waste, and faster adaptation to market changes using predictive modeling capabilities.
Can data analytics help in reducing supply chain costs?
Yes, data analytics helps reduce supply chain costs by identifying process and workflow inefficiencies, excessive overheads, potential savings opportunities through spend analytics, storage needs through inventory optimization and transportation costs via enhanced logistics network visibility.
How does predictive analytics improve inventory management?
Predictive analytics improves inventory management by forecasting demand more accurately weeks or months in advance, allowing businesses to calibrate stock buildups, warehousing capacities and logistics contracts that cost-optimize inventory availability aligned to projected requirements.
What role does data analytics play in demand forecasting?
Data analytics plays an integral role in demand forecasting by aggregating consumption trends, pricing signals, channel sales data, events sentiment analyses and leading economic indicators then applying algorithms on the consolidated information to reliably predict future demand across weeks and months.
How can data analytics enhance supplier management?
Data analytics enhances supplier management by tracking thousands of external signals – financial distress indicators, leadership moves, ratings downgrades, bankruptcies and meteorological or geopolitical disruptions – alerting supply chain teams about at-risk vendors months earlier and allowing preemptory pivoting.
What technologies support data analytics in supply chain optimization?
Core technologies supporting supply chain analytics include IoT sensors, blockchain distributed ledgers, cloud data lakes and warehouses, machine learning algorithms, advanced analytics tools and customized data visualization dashboards conveying insights extracted from statistical modeling, simulations, and predictive techniques.
What challenges might companies face when implementing data analytics in their supply chain?
Implementation challenges include poor data quality, fragmented information silos preventing consolidation, talent recruitment hurdles finding qualified data professionals, embedding insights adoption resistance from functional teams, lack of automation seamlessly translating findings into actions and cultural aversion towards data-evidenced decision-making over status quo intuition.
How can businesses overcome barriers to adopting supply chain analytics?
Strategies overcoming adoption barriers include implementing master data governance, dismantling data fiefdoms through C-suite decrees, exploring machine learning assisted modeling, incorporating usage KPIs into evaluations, automating responsive actions based on analytical alerts and appointing change management teams securing stakeholder buy-in at scale.
What are some examples of successful supply chain optimization through data analytics?
Reported examples include IBM predicting demand surges for prioritizing production and shipments ahead of hurricanes, UPS optimizing drop-off routes saving millions, Nike applying predictive analytics minimizing stock-outs, Walmart boosting on-shelf availability 4% via analytics and Amazon leveraging ML dramatically cutting forecasting errors enterprise-wide post adoption.